1. 서 론
2. 3.6 m급 토압식(EPB) 쉴드TBM을 이용한 실대형 굴진시험
2.1 실대형 굴진시험 설비 및 실험계획
2.2 실험용 쉴드TBM의 커터헤드 설계
2.3 실험용 쉴드TBM의 커터헤드 구동부 설계
3. 실대형 쉴드TBM 굴진실험을 통한 순굴진율 모델 개발
3.1 디스크커터 당 연직력과 압입깊이의 상관모델 제안
3.2 디스크커터 연직력과 회전력의 상관모델 개발
4. 쉴드TBM의 구동부 성능 이해 및 최적운전 조건 제시
4.1 쉴드TBM의 구동부 성능 및 순굴진율 향상 방안
4.2 암반조건별 쉴드TBM 최적 운전방안 제시
5. 결 론
1. 서 론
송전선로 지중화사업의 확대에 따라 도심지 및 고수압 해저구간 등을 통과하는 터널식 전력구가 지속적으로 증가하고 있다. 2000년대 이후부터 현재까지 약 200 km 연장의 터널식 전력구가 건설되었으며, 지난 20년간 매년 약 6 km씩 연장이 증가하고 있는 추세이다. 국내의 터널식 전력구는 주로 3.6 m급 쉴드TBM (Tunnel Boring Machine) 장비를 이용하여 약 7 m2 면적의 지하공간을 창출한다. 터널식 전력구의 공사기간 및 공사비를 산정하기 위해서는 쉴드TBM 장비의 굴진성능과 암반분류별 순굴진율을 정확히 예측하여야 한다. 더불어, 정해진 공사일정을 달성하기 위해서는 다양한 암반구간별 쉴드TBM 장비의 효율적인 운전이 수행되어야 한다. 이를 위해서는 암반의 공학적 특성과 장비의 운전조건에 대한 이해가 필수적이다. 쉴드TBM 장비의 소요추력, 토크, 동력, 그리고 커터헤드 회전속도와의 상관관계를 종합적으로 고려해야 한다.
국내에서는 쉴드TBM의 순굴진율을 산정하고, 암반에 따른 장비의 기본적인 사양을 설계할 시 대표적으로 CSM (Colorado School of Mines) 모델(Rostami, 1997)과 NTNU (Norwegian University of Science and Technology) 모델(Bruland, 2000)을 많이 사용한다. 선행연구(Jo et al., 2019; La et al., 2019; Chong et al., 2020; Kim et al., 2020b)에서 위 모델들의 장 ‧ 단점에 대해 많은 분석을 수행하였다. 한전 전력연구원(KEPRI)에서는 정확한 공사기간 및 비용을 산정하기 위하여 다양한 전력구 현장의 굴진데이터(지반 및 기계데이터) 활용을 통해 순굴진율 모델을 구축하고자 하는 노력을 지속적으로 해왔다(Kim et al., 2018; Jo et al., 2019). 또한, 국내 연구단에서는 머신러닝(적응형 뉴로퍼지 추론 시스템 등)기법을 통해 현장 데이터를 활용하여 시공된 순굴진율을 학습하고, 잔여구간에 대해 높은 예측정확도를 달성한 사례가 있다(KAIA, 2020). 그러나 굴진데이터를 활용한 통계분석 방법들은 기존 데이터가 없거나 기존과 다른 조건에서는 설계단계 시 범용적으로 사용하는데 한계점이 있다. 그리고 해저구간 등에서의 제한된 지반조사 회수와 잦은 선형변경으로 인해 시추공간 사이 암반에 대한 정보가 부족하기 때문에 암반의 공학적 특성과 기계데이터를 정확히 매칭시켜 분석함에 있어 어려움이 있다. 개방형 TBM이나 지하수가 없는 건조한 암반상태에서는 전방의 암반을 맵핑하거나 샘플을 채취하여 조사할 수 있기 때문에 현장의 굴진데이터를 잘 활용할 수 있다. 반면, 국내암반에서는 토압식 및 이수가압식의 밀폐형 TBM을 주로 활용하기 때문에 어려움이 있다. 해외에서는 암반의 공학적 특성(일축압축강도 및 불연속면 특성)을 사전에 파악하여 실제암반에서 쉴드TBM의 운전조건에 따른 압입깊이와 기계데이터간 상관관계를 분석하는 연구들이 수행되었다(Gong et al., 2007; Jing et al., 2019).
본 연구에서는 한국과학기술원에 위치한 실대형 실험센터에서 국내 암반강도를 대표할 수 있는 총 4가지 다른 강도조건에서 장비의 주요 운전변수인 소요추력과 커터헤드의 회전속도에 따라 총 5회에 걸쳐 약 100번의 실험케이스을 수행하고, 3.6 m급 쉴드TBM에 적합한 순굴진율 산정방법을 제시하였다. 전력연구원의 굴진DB 관리 시스템을 활용하여 분석한 결과 국내현장에서는 설계동력 대비 최대 약 45% 정도를 사용하고 있는 것으로 파악되었다. 이는 파쇄대 등의 어려운 굴착환경, 오퍼레이터의 경험적인 운영, 그리고 재사용 장비의 사용 등의 이유로 생각해볼 수 있다. 최신 쉴드TBM 장비의 경우 실시간으로 데이터가 시각화되지만 운전현황을 직관적으로 판단할 수 있는 방법 및 도구가 부족하였다. 장비의 최적운전 조건에 대한 사항은 커터헤드 구동부의 성능곡선을 통해 표현될 수 있다. 본 연구에서는 순굴진율 모델을 이용하여 630 kW의 동력으로 설계된 커터헤드 구동부 성능곡선을 바탕으로 암반등급별 최적운전에 대해 제시하였다. 개발된 순굴진율 모델과 최적운전조건을 통해 공사기간을 단축할 수 있으며, 이로 인한 터널식 전력구 조기사용에 대한 국민편익 증대 및 민원저감 효과를 기대할 수 있다.
2. 3.6 m급 토압식(EPB) 쉴드TBM을 이용한 실대형 굴진시험
2.1 실대형 굴진시험 설비 및 실험계획
본 연구에서는 단일의 디스크커터를 이용한 선형 및 회전절삭시험이 아닌 실대형 커터헤드를 암반에 압입하여 3.6 m급 쉴드TBM의 전반적인 굴진성능 분석을 통해 순굴진율 모델을 개발하고자 하였다. 다양한 디스크커터의 종류(센터, 페이스, 게이지)와 설치간격 및 각도를 종합하여 하나의 시스템으로 분석을 수행하고자 하였다. 커터헤드 직경의 크기를 고려하여 인공암반의 크기는 87.5 m3 부피(폭: 5 m, 높이: 5 m, 종방향 길이: 3.5 m)로 제작하였다. 실대형 굴진시험을 위한 대규모 암석시편의 절삭 및 운반 등의 한계점을 인식하고, 콘크리트와 모르타르를 통하여 인공암반을 조성하였다. 인공암반의 재료는 선행연구(Geng et al., 2016; Peng et al., 2018) 고찰을 통해 결정하였으며, 인공암반의 큰 장점으로는 균질한 일축압축강도를 조성할 수 있기 때문에 일축압축강도가 굴진성능에 미치는 영향에 대해서 명확히 파악할 수 있다.
Fig. 1은 구축된 실대형 굴진시험 시설을 나타낸다. 공동구 연구단을 통해 한전 전력연구원, 한국과학기술원, 이엠코리아가 공동으로 장비제작 및 시험시설을 구축하였다. 시험시설은 크게 3가지 부분으로 나뉠수 있다. 3.6 m급 EPB 쉴드TBM이 추력을 통해 굴진을 수행할 수 있도록 전반적인 지지와 반력벽의 역할을 하는 강재구조물과 인공암반을 조성할 수 있는 암반박스, 그리고 3.6 m급 EPB 쉴드TBM (구동부 유압설비 및 배토를 위한 컨베이어 벨트 등 포함)이다.
본 연구에서는 암반의 일축압축강도와 장비의 소요추력 및 커터헤드 회전속도에 따른 순굴진율 모델을 개발하고자 실대형 굴진시험을 다음 Table 1과 같이 계획하였다. 일축압축강도는 터널식 전력구 현장에서 가장 많은 빈도수를 보이고 있는 20, 50, 70, 100 MPa로 계획하였고, 조성된 인공암반의 재료와 계획 대비 실제 조성된 일축압축강도 시험결과는 Table 1에서 확인할 수 있다. Fig. 2에서와 같이 인공암반을 조성하였다. #Test 2는 50 MPa의 동일강도 내에서 인공암반의 재료를 콘크리트와 모르타르로 각각 수행하였다. 본 연구에서는 인공암반의 재료가 굴진성능에 미치는 영향에 대한 결과는 포함하고 있지 않으며, 50 MPa의 경우 두 인공암반 재료에서 수행된 결과를 종합하여 분석하였다. Table 2에서와 같이 소요추력 조건은 디스크커터의 개수(17인치 26개 사용)와 허용하중 및 쉴드잭 유압설비 등을 고려하여 1,000 kN부터 5,000 kN까지 총 5가지 운전조건으로 설정하였다. 여기서, 소요추력을 디스크커터의 개수로 나누어보면 디스크커터 당 작용하는 평균 연직력은 38.46 kN부터 192.31 kN으로 계산할 수 있다. 또 다른 주요 운전조건인 커터헤드 회전속도는 구동부의 성능을 고려하여 총 4가지 운전조건(1.5 RPM, 4.5 RPM, 6.0 RPM, 7.5 RPM)으로 설정하였다. 암반강도 및 소요추력에 따라 목표 커터헤드 회전속도를 맞추기 위하여 시행착오를 통해 가동할 유압펌프의 개수를 정하였다. 총 4가지의 암반강도 내에서 총 20개의 운전조건을 고려하여 약 100회의 실험을 수행하였다. 1회당 굴진거리는 약 50 mm에서 100 mm사이로 설정하여 실험을 수행하였다.
Table 1.
Test cases according to stength of artificial rock sample and TBM operational parameters
Test cases | Artificial rock sample | TBM operational parameters | ||
Material | Planned UCS | Measured UCS | ||
(MPa) | ||||
#Test 1 | Mortar | 20 | 27 | Table 2 (It can be varied according to torque-RPM relationships) |
#Test 2 | Concrete | 50 |
57
(average) | |
Mortar | ||||
#Test 3 | Concrete | 70 | 70 | |
#Test 4 | Mortar | 100 | 99 |
Table 2.
TBM operational parameters for stepwise tunnelling (Kim et al., 2020b)
막장압의 영향을 최소화하여 소요추력에 따른 압입깊이 상관관계를 도출하고자 토압계에 작용하는 챔버압을 모니터링하여 스크류컨베이어 속도를 증가시켜 빠르게 배토를 수행한 오픈모드(Open mode)로 운전을 수행하였다. 오퍼레이터룸에서는 쉴드TBM의 소요추력, 굴진거리, 굴진시간, 커터헤드 회전속도, 유압펌프의 압력(토크와 관련), 피칭(Pitching), 구동부 씰의 온도, 챔버압, 쉴드잭 및 중절잭 압력 등의 정보가 매 5초마다 저장되도록 설정하였다.
2.2 실험용 쉴드TBM의 커터헤드 설계
커터헤드는 275 MPa의 항복강도를 가지는 SS275를 용접하여 용접형의 커터헤드를 제작하였다. 커테헤드 외경은 3,560 mm로 터널식 전력구의 세그먼트 내경 3,000 mm를 설치할 수 있도록 설계하였다. 총 26개의 17인치 직경 디스크커터를 배열하여 평균 68.5 mm의 절삭간격을 가지도록 제작하였다. Fig. 3과 같이 총 6개로 구성된 센터 디스크커터는 각 커터간 84 mm의 절삭간격을 가지도록 설계하였다. 그리고 총 12개로 구성된 페이스 디스크커터는 각 커터간 80 mm의 절삭간격을 가지도록 설계하였다. 게이지 커터는 굴착직경 3,622 mm의 확보와 R30 m의 급곡구간을 회전할 수 있도록 총 8개로 구성하였다. 최대 65 mm에서 최소 20 mm의 절삭간격으로 설계하여 최외각의 커터일수록 설치각도에 따른 하중의 분포를 고려하여 절삭간격을 감소시켰다. 개구율은 약 19.3%로 설계하였다. Fig. 3과 같이 굴착된 인공암반 칩을 파쇄할 수 있도록 콘 크러셔를 제작하였다. Fig. 4는 제작된 케터헤드로 실험 중 인공암반 내 굴착면의 모습을 보여준다.
2.3 실험용 쉴드TBM의 커터헤드 구동부 설계
다음 Fig. 5는 실험용 쉴드TBM의 커테헤드 구동부와 쉴드잭을 작동하기 위한 유압설비, 오퍼레이터룸, 냉각 시스템 등을 나타내었다. 유압설비는 구동부에 토크발현과 커터헤드를 회전시키기 위한 7개의 유압펌프를 포함하고 있다. 터널식 전력구 공사 시 많이 사용되는 440 kW와 630 kW의 두 동력 중 큰 토크발현에서도 다양한 커터헤드 회전속도를 구현하여 실험을 수행할 수 있도록 동력의 크기를 630 kW로 설정하였다. 각 1개의 유압펌프는 90 kW의 동력으로 설계되었다. 총 7개의 유압펌프를 통해 최대 630 kW의 동력 내에서 최대토크 및 최대 커터헤드 회전속도로 굴진을 수행할 수 있다. 커터헤드로 유입되는 암반 칩이나 최대 5 bar 수압에 대응하기 위한 구동부 VD 씰(Seal)에 그리스와 냉각수를 공급해주기 위한 설비들도 갖추어져 있다. 오일탱크로부터 최대 32 bar의 압력을 통해 5개의 유압모터롤 전달되어 최대 1,309 kN ‧ m의 토크까지 발현할 수 있도록 설계되었으며, 최대 400 L/min의 유량을 통해 최대 10.5 RPM까지 회전할 수 있도록 설계하였다. 자세한 구동부 유압설비 사양은 선행연구(Kim et al., 2020b)를 통해 제시하였다.
3. 실대형 쉴드TBM 굴진실험을 통한 순굴진율 모델 개발
3.1 디스크커터 당 연직력과 압입깊이의 상관모델 제안
쉴드TBM의 순굴진율을 산정하기 위해서는 우선 압입깊이를 산정해야 한다. 압입깊이는 암석의 일축압축강도와 장비의 소요추력(암반에 압입하는데 필요한 추력)에 의해 결정되게 되며, 본 연구에서는 단일 디스크커터가 아닌 전체 커터헤드의 평균적인 굴진거리를 바탕으로 압입깊이를 산정하였다. 압입깊이는 쉴드잭의 이동속도를 굴진구간 내 평균 커터헤드 회전속도로 나누어 산정하였다. 소요추력을 총 디스크커터의 개수로 나누어 디스크커터 당 평균 연직력과 압입깊이와의 상관관계를 다음 Fig. 6에 나타내었다. 암반강도별로 디스크커터 당 연직력이 증가함에 따라 압입깊이가 지수함수 형태로 증가하는 경향을 보였다. 암반의 일축압축강도가 작아짐에 따라 압입깊이는 뚜렷하게 증가하는 형태를 보였다. 본 연구의 실대형 굴진실험 결과들을 바탕으로 최소자승법을 이용하여 NTNU 모델(Bruland, 2000)의 기본관계식 (1)을 통해 곡선을 피팅하여 제안하였다.
여기서, 는 압입깊이(mm/rev), 는 디스크커터에 작용하는 연직력(kN), 는 1 mm/rev을 압입하는데 필요한 임계 연직력(kN), 는 지수함수 형태를 나타내는 압입지수이다.
압입깊이 산정식 (1)은 [디스크커터 당 연직력, Fn]을 [1 mm/rev을 압입하는데 필요한 임계 연직력, F1]으로 나눈값에 지수함수 형태를 나타내기 위한 압입지수 b의 거듭제곱 형태로 도출되었다. 압입지수 b는 해외모델에서 굴착 용이성과 TBM의 효율을 대표하지만 본 압입지수는 3.6 m급 실대형 굴진실험의 결과를 통해 산정식의 형태를 결정하는데 활용하였다. 디스크커터 당 연직력은 설계자가 판단하여 입력하는 변수로써, 디스크커터 제작사에서 제시한 시험인증서의 값을 사용하도록 권장한다. 압입깊이는 현장자료를 참고하여 상한값은 8 mm/rev 이하로 제한하여 사용하는 것을 추천한다. 또한, 암석의 일축압축강도가 30 MPa 이상에서만 사용하는 것을 권장한다. 그 이유는 실대형 굴진실험 시 최소 약 30 MPa의 강도에서 수행되었으며, 해외모델의 경우에는 강도가 약한 암반에서는 예측 정확도가 크게 감소하기 때문이다. 이에 본 연구에서는 #Test 1, #Test 2, #Test 4의 결과로 도출된 디스크커터 당 연직력과 압입깊이의 상관관계 추세선(Fig. 7의 수식)을 바탕으로 풍화암(30 ≤ UCS < 50), 연암(50 ≤ UCS < 100), 경암(100 ≤ UCS)으로 분류하여 다음 Fig. 7과 같은 디스크커터 당 연직력과 압입깊이의 상관관계 도표를 제안하였다.
커터헤드의 회전속도는 순굴진율을 증가시키는 직접적인 방법이지만 커터헤드의 분당 회전수인가 압입깊이에 미치는 영향에 대해서는 아직 명확하게 규명되지 않았다(Kim et al., 2020a). 본 연구의 수행결과 디스크커터 당 연직력과 압입깊이의 상관관계에서는 커터헤드의 회전속도는 다음 Fig. 8과 같이 다양한 암반강도에서 압입깊이에 미치는 영향이 매우 미비한 것으로 판단되었다(Kim et al., 2020a). 커터헤드 회전속도는 압입깊이에 영향을 주는 인자보다는 압입깊이에 영향을 받은 인자로 판단할 수 있다.
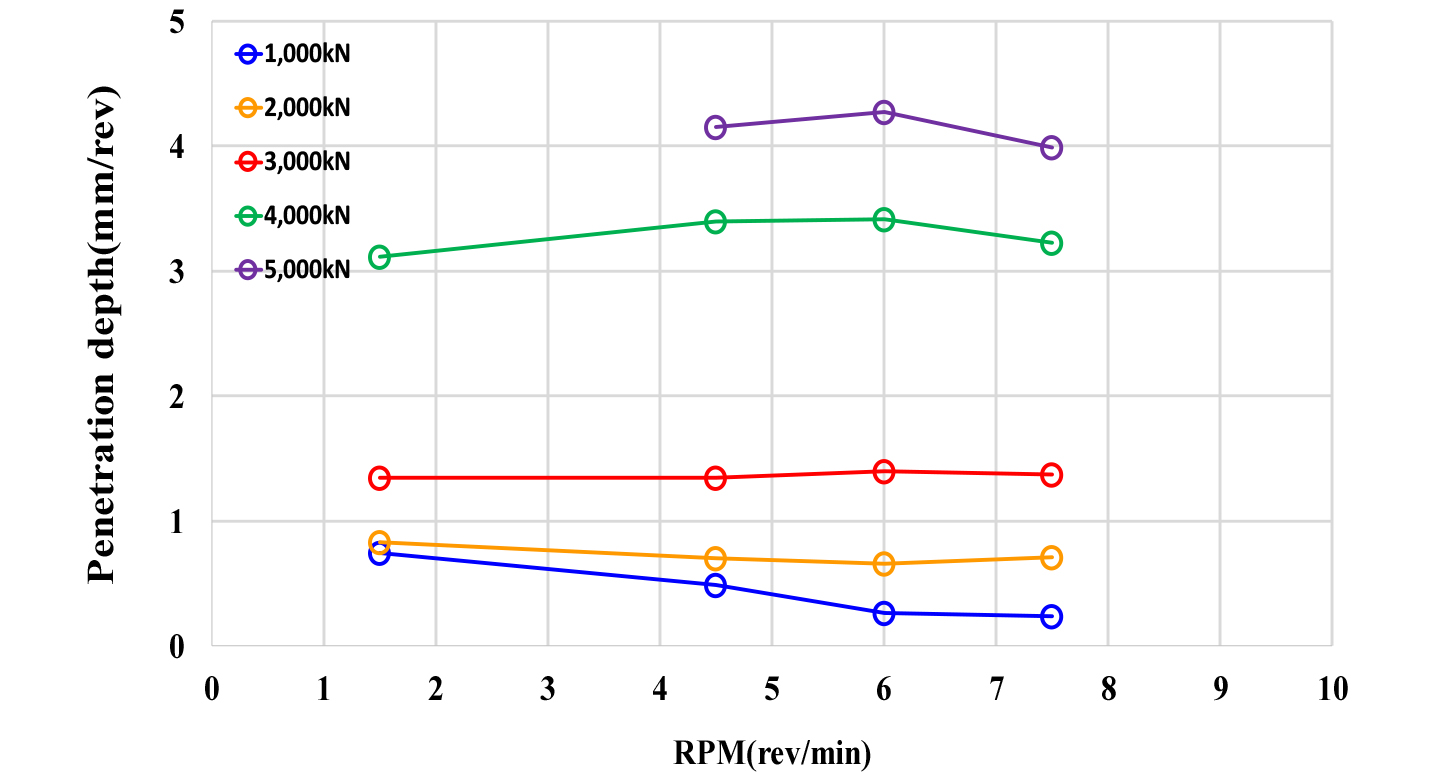
Fig. 8
Relationships between RPM and penetration depth at different thrust force levels based on test results (Kim et al., 2020a)
3.2 디스크커터 연직력과 회전력의 상관모델 개발
다음 Fig. 9와 같이 동일한 커터헤드 회전속도 내에서 암반의 다양한 일축압축강도에서 소요추력과 토크는 뚜렷한 선형적인 상관관계를 나타낸다. 선행연구를 통해서 소요추력과 토크와의 상관관계에서 일정 커터헤드 회전속도 이상에서는 유사한 경향을 나타낸다는 것을 고찰하였다. 다만, 커터헤드의 회전속도가 매우 작은 RPM 조건(1.5 RPM)에서는 다소 큰 토크가 발현될 수 있음을 확인하였다. 작동한 쉴드잭에 개수에 따라서도 토크의 크기에 영향을 받을 수 있음을 확인하였다(Kim et al., 2020b). Fig. 9에서와 같이 암반의 일축압축강도가 작아질수록(Test case에 따라) 동일 소요추력 대비 더 큰 토크가 발현되는 것을 확인할 수 있다.
위 소요추력과 토크와의 상관관계를 바탕으로 다음 식 (2)와 (3)을 이용하여 디스크커터에 작용하는 평균 연직력과 평균 회전력의 관계로 나타내었다.
여기서, 는 소요추력(kN), 는 디스크커터의 개수, 는 디스크커터에 작용하는 회전력(kN), 는 토크(kN ‧ m), 는 디스크커터의 상대적 거리계수(약 0.6을 사용), 는 커테헤드의 직경(m)이다.
암반강도별(Test cases)로 쉴드TBM 운전조건 4.5 RPM 이상에서의 디스크커터 당 연직력과 회전력의 상관관계를 종합하여 분석하였다. 암반강도가 작은 경우 630 kW의 동력 내에서 토크와 회전속도의 상관관계에 의해서 수행할 수 없었던 시험과 쉴드잭의 영향이 있는 결과는 본 분석에서 제외하였다. 암반조건별 연직력과 회전력의 상관관계에서 결정계수는 0.71에서 0.89로 도출되었고, 4.5, 6.0, 7.5 RPM 조건 등을 종합하여 분석하였기 때문에 소요추력과 토크의 상관관계보다 다소 결정계수가 감소된 것을 확인할 수 있다. 다음 식 (4)와 같이, 도출된 디스크커터 당 연직력과 회전력의 상관관계 중 연직력 대비 회전력의 비(추세선의 기울기)를 분석하였다. Fig. 10에서와 같이 암반강도가 증가함에 따라 kc의 값은 0.095에서 0.055로 크게 감소하는 것을 확인할 수 있다.
여기서, 는 디스크커터의 연직력과 회전력의 비이다.
본 연구에서는 Fig. 10의 결과와 식 (3)을 이용하여 토크를 산정하고, 암반의 일축압축강도와 디스크커터의 연직력의 크기에 따라 다음 Fig. 11의 토크 설계도표를 제안하여 장비의 사양을 설계 및 검수 시 활용할 수 있도록 하였다. 터널식 전력구에서 대표적인 쉴드TBM의 커터헤드 직경을 3.6 m로 설정하고, 디스크커터의 개수를 26개로 설정하여 도식화하였다(다양한 장비성능에 따라 도식화가 가능하다). 디스크커터에 동일한 연직력이 작용하였을 때, 암반의 일축압축강도가 작아질수록 압입깊이가 증가하여 토크가 크게 발현되는 것을 확인할 수 있다. 디스크커터의 연직력의 크기가 증가함에 따라 토크도 크게 증가하여 발현되는 것을 확인할 수 있다. 17인치 디스크커터의 허용 연직력의 크기인 200 kN을 적용하였을 때, 일축압축강도 최소 30 MPa에서 최대 200 MPa 사이에서 토크는 약 430 kN ‧ m에서 690 kN ‧ m의 범위가 도출되게 된다. Fig. 11의 일축압축강도와 토크와의 상관관계를 통해 630 kW 동력 내에서의 일축압축강도와 커터헤드 회전속도와의 상관관계를 다음 Fig. 12에 나타내었다. 일축압축강도가 증감함에 따라 토크와는 반대로 커터헤드 회전속도는 증가하며, 작용한 디스크커터 당 연직력의 크기가 감소함에 따라 커터헤드 회전속도가 증가하는 경향을 나타내었다. 장비의 최대 커터헤드 회전속도를 고려하여 최대값을 제한하여 적용할 수 있다.
4. 쉴드TBM의 구동부 성능 이해 및 최적운전 조건 제시
4.1 쉴드TBM의 구동부 성능 및 순굴진율 향상 방안
쉴드TBM을 통하여 터널식 전력구를 시공할 시 적기가압과 효율적인 장비운전을 위해서는 장비 오퍼레이터의 역할이 무엇보다 중요하다. Fig. 13의 토크와 커터헤드 회전속도 상관관계를 통해 장비 구동부의 동작원리와 순굴진율 향상방안에 대해 생각해볼 수 있다. 유압식 모터와 펌프로 구성된 쉴드TBM은 Fig. 13과 같이 구동부가 성능을 발휘할 수 있다. 검은색 실선이 유압식 펌프 7대와 유압식 모터 5대가 발휘할 수 있는 최대 성능을 나타낸다(한전 전력연구원 보유 실험장비). 회색 점선으로 표시된 부분이 90 kW의 유압식 펌프 각 1대당 발휘할 수 있는 성능이 된다. 이에 작동하는 유압펌프의 개수가 증가함에 따라 발휘할 수 있는 구동부 성능은 향상된다. 구동부 성능곡선을 작도하기 위해서는 펌프에서 작용하는 유압의 크기에 따른 유압모터 1대당 토크성능, 유압모터 및 펌프 사양, 장비의 효율(%) 등의 세부정보가 필요하다.
소요추력에 의해 토크가 발현되게 되면 일정 동력 내에서 커터헤드 회전속도가 결정되게 된다. 토크가 크게 발현되지 않을 경우 동력의 크기 내에서 커터헤드 최대 회전속도는 일정하게 유지되다가 토크가 일정 크기 이상 발현됨에 따라 커터헤드 회전속도는 다음 식 (5)에 따라 반비례 형태로 감소하게 된다.
여기서, 은 커터헤드의 회전속도(rev/min), 는 구동부 동력(kW), 는 장비의 효율(%)이다.
Fig. 13의 토크와 커터헤드 회전속도의 상관관계에서는 높은 추력조건인 4,000 kN와 5,000 kN 조건에서는 낮은 추력조건과 비교하여 동일한 커터헤드 회전속도로 운전하기 위해서는 더 많은 수의 유압펌프를 가동(높은 동력)해야 하는 것을 확인할 수 있다. 예를 들어 추력 3,000 kN에서 6.0 RPM급의 커터헤드 회전속도를 내기 위해서는 1.5 RPM씩 설계된 유압펌프 4개를 작동하였다면, 추력 4,000 kN 조건에서는 5대 혹은 6대를 작동해야 하는 것을 의미한다. Fig. 13의 토크와 동력과의 상관관계에서 소요추력의 크기가 1,000 kN에서 장비를 운전했을 때보다 소요추력을 증가시켜 4,000 kN과 5,000 kN으로 장비를 운전할 때 동력의 크기가 더 잘 활용되는 것을 확인할 수 있다. 즉, 토크와 동력과의 상관관계로 살펴보게 되면, 일정 토크 이상이 발현 되어야만 유압펌프 대당 동력을 최대로 사용할 수 있게 된다. 순굴진율 향상을 위한 운전방안에 대해 살펴보면, 추력 1,000 kN과 1.5 RPM 조건(유압펌프 1대 가동, 파랑색 원 기호)에서는 Fig. 13에서와 같이 70 MPa급 암반(#Test case 3)에서 약 0.74 mm/rev의 압입깊이가 도출되게 된다. 반면에 추력 5,000 kN과 약 7.5 RPM 조건(유압펌프 7대 가동, 보라색 원 기호)에서는 약 3.98 mm/rev의 압입깊이가 도출되어 약 5.4배의 압입깊이 향상 효과를 나타낸다. 이와 더불어 커터헤드의 회전속도도 1.5 RPM에서 7.5 RPM으로 5배가 증가했기 때문에 순굴진율(mm/min)은 최대 27배(5.4배×5배)의 증가효과를 가져오게 된다.
4.2 암반조건별 쉴드TBM 최적 운전방안 제시
본 연구에서는 제안된 순굴진율 산정방법을 통해 암반조건을 풍화암 및 연 ‧ 경암으로 분류하여 순굴진율을 향상시키고, 장비의 능력을 활용할 수 있는 최적운전 방안에 대해 제시하고자 한다. 제안된 순굴진율 산정방법을 활용하기 위하여 다음 Table 3의 11곳의 현장의 일축압축강도를 활용하여 최소 및 최대토크를 계산하였다. 11곳의 현장의 암반강도에 따라 최대 일축압축강도 293 MPa에서 최소 303 kN ‧ m의 토크가 발현되었고, 최소 일축압축강도 32 MPa에서 최대 822 kN ‧ m의 토크가 발현되었다. 이를 현장에서 도출할 수 있는 최소 운전토크 300 kN ‧ m, 최대 운전토크 800 kN ‧ m으로 산정하였다.
Table 3.
Frequency of rock mass classification and torque estimation at each construction site
Fig. 14를 살펴보면 장비 성능곡선 내 운전영역 A와 운전영역 B로 구분하였다. 이와같은 운전영역은 본 연구에서 제안한 순굴진율 모델을 활용하여 제안되었다. 운전영역 A는 장비의 효율을 고려하여 커터헤드 최고 회전속도의 80%의 성능까지 회전가능하고, 토크는 경계토크 이내에서 운전가능한 영역으로 정의하였다. 여기서, 경계토크란 커터헤드의 최대회전속도로 회전할 수 있는 최대 토크를 말한다. 경계토크 이상 발현이 된다면 커터헤드 회전속도는 저하되게 된다. 운전영역 A 경계선의 정의는 다음과 같이 정리하였다. 최소 운전토크는 총 11현장의 암반조건 내에서 본 연구에서 개발한 순굴진율 모델을 통해 최소 운전토크를 산정하였다. 특히, 경암의 경우에는 일반적으로 압입깊이가 작아 토크가 크게 발현되지 않기 때문에 운전영역 A에서 커터헤드 회전속도를 증가시켜 장비를 운전하는 것을 권장한다.
∙ 운전영역 A 경계 : ① 최소 운전토크 : 300 kN ‧ m (11현장조건으로 분석)
② 경계토크
③ 최소 운전RPM : 최대 운전토크와 동력의 80% 성능 내 RPM
④ 최대 운전RPM : 장비 최대 RPM의 80%
일반적으로 순굴진율 향상과 장비의 성능을 최적으로 활용하기 위해서는 기본적으로 운전추력을 증가시켜 디스크커터의 압입깊이를 증가시키고, 토크를 운전영역 B 내에서 발현될 수 있도록 해야한다. 풍화암 및 연암의 경우에는 Fig. 14의 운전영역 B에서 쉴드TBM 장비를 운전하는 것을 권장한다. 운전영역 B의 경계선의 정의는 다음과 같이 정리하였다. 최대 운전토크는 총 11현장의 암반조건 내에서 본 연구에서 개발한 순굴진율 모델을 통해 최대값을 산정하였다. 이 최대 운전토크를 이용하여 터널식 전력구 공사에 많아 적용되고 있는 630 kW 동력의 80%를 고려하여 식 (5)를 통해 최소 운전RPM을 산정하였다. 단, 제시한 최적 운전방안은 본 연구에서 개발한 순굴진율 모델만을 바탕으로 제시하였으며, 특수한 암반조건과 다양한 장비의 사양에 따라 활용에 제한을 가질 수 있다.
∙ 운전영역 B 경계 : ① 경계토크
② 최대 운전토크 : 800 kN ‧ m (11현장조건으로 분석)
③ 최소 운전RPM : 최대 운전토크와 동력의 80% 성능 내 RPM
④ 최대 운전RPM : 장비 최대 RPM의 80%
5. 결 론
본 연구는 터널식 전력구 설계 및 시공 시에 공사기간과 공사비용의 예측정확도를 향상시키고, 3.6 m급 쉴드TBM에 적용할 수 있는 범용적 순굴진율 개발 및 이를 이용한 최적운전 조건을 제시하였다.
1.3.6 m급 실대형 굴진시험을 통하여 터널식 전력구 공사에 활용할 순굴진율 모델을 개발하였다. 소요추력으로 계산한 디스크커터 당 평균 연직력과 장비의 굴진거리로 계산한 평균 압입깊이를 이용하여 디스크커터와 암반 일축압축강도의 크기를 고려할 수 있는 연직력과 압입깊이와의 상관관계를 도출하였다. 풍화암, 연암, 경함분류를 통해 도식화하여 제안하였다. 본 산정식은 5,000 kN의 추력조건까지 수행된 결과로 도출되었으며, 향후 그 이상 추력조건을 바탕으로 상관관계를 업데이트할 계획이다.
2.소요추력과 토크와의 선형적인 상관관계를 통하여 디스크커터 당 작용하는 평균 연직력과 회전력의 상관관계를 도출하였다. 연직력 대비 회전력의 비(kc)를 도출하여 3.6 m급 쉴드TBM (630 kW 동력)에서 활용할 수 있는 일축압축강도와 토크 및 일축압축강도와 커터헤드 회전속도의 설계도표를 제시하였다.
3.실대형 굴진시험 결과를 바탕으로 순굴진율 향상방안에 대해 고찰하였다. 소요추력과 유압펌프의 개수를 증가시켜 운전한 결과 최대 약 27배의 순굴진율 향상 효과를 확인하였다. 동일한 유압펌프를 가동하더라도 소요추력을 증가시켜야만 동력을 최대한 활용할 수 있음을 구동부 성능곡선을 통해 확인하였다.
4.현장의 암반강도를 바탕으로 순굴진율 모델을 활용하여, 구동부 성능곡선 내 암반분류별 최적 운전조건에 대해 제시하였다. 현장에서 도출할 수 있는 최대(최소) 운전토크를 산정하고, 구동부 효율을 고려하여 최대(최소) 운전 커터헤드 회전속도를 산정하였다. 터널식 전력구 시공 시 실시간으로 기계데이터를 모니터링하여 구동부의 성능(노후화 장비에 따라 효율고려)을 최대한 활용한다면 공사기간 단축 등의 긍정적인 효과가 기대된다.