1. 서 론
2. 뒷채움재 종류
2.1 주재료
2.2 화학 첨가제
3. 뒷채움재 내구성 평가를 위한 기본물성 분석사례
3.1 압축강도(compressive strength)
3.2 밀도(density)
3.3 압축율(compressibility)
3.4 투수계수(permeability)
4. 지반 조건에 따른 뒷채움 시공사례: 내구성을 중심으로
5. 결 론
1. 서 론
최근 도심 지역에서 전력구를 포함한 대중교통 시설, 상하수도 등의 인프라 건설을 위한 지하 공간 활용이 활발해짐에 따라 터널 공법의 사용이 증가하고 있다. 터널은 발파식 굴착과 기계식 굴착 방식을 통하여 시공되고 있다. 기존의 발파식 터널 굴착 공법은 소음과 진동 문제로 인해 인구 밀집 지역인 도심에 적합하지 않으므로, 기계식 굴착공법의 하나인 쉴드 TBM (tunnel boring machine) 공법의 적용이 증가하는 추세이다.
쉴드 TBM 공법을 이용한 터널 굴착 후 콘크리트 라이닝이 설치되며, 이러한 콘크리트 라이닝은 지하수 차단, 주변 지반으로부터 분리, 차량 통행에 따른 시계 및 미관 확보 등을 위하여 활용된다(Han and Jeong, 2014). 또한, 콘크리트 라이닝을 설치하는 과정에서 라이닝과 굴착된 지반 사이에 필연적으로 배면공동 또는 테일 보이드(tail void)라는 공간이 형성된다(Fig. 1). 이러한 배면공동을 장기간 방치하는 경우, 터널 내부로의 지하수가 유입되거나 터널 주변 지반침하 및 콘크리트 라이닝의 손상과 같은 문제가 발생할 수 있다(Kim, 2010).
이러한 배면공동을 위한 보강 공법으로 뒷채움 주입방법이 널리 사용되고 있다. 뒷채움 공법이란 터널 굴착 후 굴착된 지반과 콘크리트 라이닝 사이에 시멘트 또는 화학적 기반 재료를 채워 지반 침하 및 지하수 유입 방지, 콘크리트 라이닝 보호 등 터널 구조의 안정성과 내구성을 증진시키는 방법이다(Jiang et al., 2023). 뒷채움재는 터널 배면공동 내 주입된 후 시간 경과에 따라 경화되어 터널 내 작용하는 상부 지반의 압력을 지지하는 역할을 한다. 따라서 이러한 뒷채움재의 성능을 효과적으로 발현하기 위해서는 뒷채움재의 경화 후 역학적 특성과 관련된 내구성이 중요하게 고려되어야 한다.
하지만 이러한 터널 배면공동 뒷채움을 위한 정량적인 기준 및 이에 대한 연구는 제한적인 실정이다. 국내의 경우, 국토교통부에서 제시된 터널 설계기준 TBM 터널(KDS 27 25 00)에 따르면 뒷채움재를 위한 세부 재료 및 특성이 대략적으로만 제안될 뿐 공학적인 특성이 정량적으로 제안되어 있지 않다. 해당 기준에서는 현장 조건을 고려하여 시멘트 기반 재료, 석회 및 골재를 현장 조건에 가장 적합한 재료를 선정해야 한다고 제안한 바 있다(MOLIT, 2023). 또한, 목표 강도 조기 발현 및 체적감소가 적은 재료 선정과 같이 공학적인 특성이 정량적으로 제시되어 있지 않는 실정이다. 이와 유사하게 해외 사례에서 일본의 경우, 일본토목학회 터널 표준시방서 쉴드 공법편에서는 뒷채움재는 재령 1시간 강도 0.1 MPa 및 28일 강도 2.5 MPa의 기준만을 제시하고 있는 제한적인 상황이다(JSCE, 1996).
터널을 장기적으로 안전하게 활용하기 위해서는 배면공동 내 뒷채움재가 밀실하게 충진되어 내구성을 확보하는 것이 중요하다. 만약 뒷채움재가 밀실하게 충진되지 못하고 이에 따라 체적변형 및 강도 저하로 인하여 내구성이 보장되지 않는다면 콘크리트 라이닝의 손상이 발생할 수 있다. 하지만 이러한 주입이 완료된 뒷채움재의 내구성은 육안으로 평가가 어렵기 때문에 직접적으로 뒷채움재 주입 성능을 평가하는데 한계가 있다. 이를 위하여 뒷채움재의 압축강도(Yang et al., 2022), 밀도(Mao et al., 2020)와 같은 내구성 관련 평가를 위한 실내실험이 수행된 바 있다.
본 연구에서는 터널 배면공동 뒷채움재 성능 평가를 위한 기술현황 사례를 뒷채움재의 내구성(압축강도, 밀도, 압축율, 투수계수)을 중심으로 조사 및 분석하였다. 이를 위하여 현재 수행되고 있는 뒷채움 주입현장 및 관련 연구에서 사용되는 뒷채움재의 종류에 대하여 정리하였다. 또한, 뒷채움재 내구성 평가와 관련된 기술현황 사례를 정리하였으며, 뒷채움 시공사례를 참고하여 지반 조건에 따른 뒷채움재 내구성 관련 기술을 분석하였다. 본 연구를 통하여 기술된 뒷채움재 기술현황은 향후 터널 시공 시 뒷채움재의 내구성 기준 마련을 위한 기초자료로 유용하게 활용될 것으로 기대된다.
2. 뒷채움재 종류
뒷채움재는 재료 특성 또는 주입 방식 등에 따라 분류할 수 있다. 본 고에서는 뒷채움재의 ‘내구성’ 평가를 위하여 재료 특성에 따라 뒷채움재를 분류하고자 한다. 뒷채움재는 재료 특성에 따라 주재료와 화학첨가제로 구성되며 이는 적용환경이나 목적에 따라 달라질 수 있다(Fig. 2). 주재료는 시멘트, 벤토나이트, 골재, 석회 등으로 구성되며, 화학첨가제는 규산나트륨, 감수제, 분산 저항제 및 기타 재료 등으로 구성된다(Kim, 2010; Peila et al., 2011; Mohammadzamani et al., 2023).
2.1 주재료
2.1.1 시멘트
시멘트는 터널 배면공동 뒷채움재로 가장 널리 사용되는 재료에 해당하며, 이러한 시멘트를 포함한 주재료의 경우 단독 혹은 다양한 주재료와 혼합되어 활용된다. 뒷채움을 위한 시멘트 재료는 일반 포틀랜드 시멘트(ordinary Portland cement, OPC)와 황알루미네이트 시멘트(sulphoaluminate cement)로 구분되며 함께 사용되는 경우도 있다(He et al., 2020). 일반 포틀랜드 시멘트의 경우 비용이 저렴하며 기존 콘크리트 구조물과 유사한 재료에 해당하므로 내구성이 우수하다. 황알루미네이트 시멘트 기반 뒷채움재는 일반 포틀랜드 시멘트에 비해 경화시간이 짧고 초기 강도가 높으며 미세 팽창 특성, 불투과성 및 내수식성(water corrosion resistance)이 우수하다. 이러한 시멘트 재료는 뒷채움재의 불투과성, 압축강도 및 굽힘 강도를 향상시킬 수 있으나 뒷채움재의 유동성을 상대적으로 저하시키고 주입과정에서 파이프를 쉽게 막히게 할 수 있는 단점이 있다.
시멘트 재료와 함께 초기강도 발현 또는 유동성 향상을 위하여 보조적인 시멘트계열 재료가 사용될 수도 있다. 이를 위한 재료로는 플라이 애시(fly ash), 슬래그(slag), 실리카 퓸(silica fume), 소성 점토, 미분연료재(pulverized fuel ash), 석회석 필러(limestone filler), 마이크로 실리카(micro silica), 메타카올린(metakaolin) 등이 있다(Wang et al., 2018).
2.1.2 벤토나이트
벤토나이트는 뒷채움재에 포함되어 부피를 팽창시키는 재료로서 공극을 감소시키고 재료분리를 방지하기 위해 사용된다(Delaleux et al., 2012; Tiedje and Guo, 2014). 벤토나이트는 일반적으로 나트륨-벤토나이트(sodium-bentonite)와 칼슘-벤토나이트(calcium-bentonite)로 구분되며, 나트륨-벤토나이트가 칼슘-벤토나이트에 비해 함수성이 우수하다(Bezuijen et al., 2009; Yoon and Mohtar, 2014). 벤토나이트의 최적 질량비는 뒷채움재 질량비 기준 약 3% 내외로 활용되는 것이 일반적이다. 또한 벤토나이트는 요변성(thixotropic property)을 갖는 재료로 뒷채움재 주입 중에는 점성도가 감소하거나 일정하지만 교란이 발생하지 않는 조건에서는 점성도가 증가하는 특성을 가진다. 하지만 벤토나이트는 함량이 과도하게 증가하는 경우 뒷채움재의 유동성을 감소시키기 때문에 뒷채움 주입성능을 저하시킬 수 있다.
2.1.3 골재
뒷채움에 사용되는 골재의 경우 규산질(siliceous), 석회질(calcareous) 또는 둥글거나 파쇄된 골재가 일반적으로 널리 사용된다(Linger et al., 2008). 특히 둥근 모래를 소량 사용하는 경우에는 뒷채움재 주입성능을 향상시키는 데 효과적이며, 파쇄된 골재를 사용하는 경우에는 단기 전단강도 확보에 유리한 것으로 알려져 있다. 또한, 실제 현장에서는 골재의 미립자 함량을 최대한 높여 우수한 입상 구조(granular skeleton)를 가진 골재를 얻기 위하여 2가지 종류 이상의 골재를 혼합하여 활용하기도 한다.
터널 배면공동 뒷채움에 사용되는 골재 중 모래는 주로 ASTM D2487 기준에 따라 중간크기(medium sand, 입경 425 µm 이상 2 mm 미만) 모래 및 조립률(fineness modulus) 2.0에서 3.0 범위에서 사용되며, 바인더-모래 비율(binder to sand ratio)은 0.5에서 1.4 범위에서 사용된다(Lim et al., 2013). 뒷채움재의 골재로 모래를 첨가하는 경우, 뒷채움재의 안정성을 향상시킬 수 있으며 블리딩(bleeding) 감소에 효과적이다. 또한 모래의 간극비는 경화시간 및 유동성에 영향을 미치며, 모래의 입도 분포는 함수비와 뒷채움재의 강도에 중요하게 영향을 미치는 인자에 해당한다(Mollamahmutoğlu and Avci, 2015).
2.1.4 석회
석회는 뒷채움재 주재료 구성 재료 중 한 가지에 해당한다. 석회는 생석회(quick lime)와 수화 석회(hydrated lime)로 분류되며, 뒷채움재의 전체 질량기준 약 5% 내외가 포함되는 것이 일반적이다(Oggeri et al., 2014). 석회는 뒷채움재의 유동성을 증진시키고 블리딩을 감소시킬 수 있는 장점이 있다. 하지만 석회는 부피 수축(volume shrinkage)을 증가시킬 수 있으며, 특히 생석회를 사용하는 경우 뒷채움재의 압축강도를 감소시킬 수 있다. 또한 석회는 뒷채움재의 경화시간에 영향을 미치는 결정적인 재료에 해당하므로 뒷채움 현장의 환경 및 목적에 부합하도록 석회의 양을 조절하는 것이 필수적이다.
2.2 화학 첨가제
터널 배면공동 뒷채움을 위하여 단순 시멘트 기반의 주재료만을 활용한 뒷채움재는 초기강도 발현 및 유동성 확보 등과 같은 한계가 있다. 이에 따라 실제 뒷채움 현장에서는 원활한 뒷채움 성능 발현 및 개선 등을 위하여 화학 첨가제와 같은 혼합 재료가 추가적으로 사용된다. 뒷채움재로 사용되는 화학 첨가제는 목적에 따라 다양하게 활용될 수 있으며, 주로 규산나트륨(sodium silicate), 감수제(superplasticizer), 분산저항제(dispersion resistance agent) 및 기타 화학 첨가제 등이 사용되고 있다.
2.2.1 규산나트륨
규산나트륨은 알칼리성 활성제로서 뒷채움재의 경화시간을 크게 단축시키는데 유용하다. 또한 급결 성능(quick-setting ability)이 우수하여 지하수가 존재하는 지반조건에서 우수한 밀폐 성능(sealing ability)을 발현할 수 있다(He et al., 2020). 또한 플라이 애시와 슬래그의 활성을 가속시키고 시멘트의 2차 수화를 촉진하여 경화체의 강도를 향상시키는데 유용하다. 하지만 규산나트륨은 뒷채움재의 내마모성(scour resistance)을 약화시키고 뒷채움재의 수축을 유발하여 내구성에 영향을 미칠 수 있다고 보고된 바 있다. 따라서 규산나트륨을 사용할 경우, 뒷채움재의 내마모성과 내구성 향상을 위해 추가적인 주재료 및 화학 첨가제와 함께 사용되는 것이 일반적이다.
2.2.2 감수제
감수제는 뒷채움재에서 가장 중요한 화학 첨가제이며 뒷채움재로 첨가되는 경우 슬럼프(slump)의 변화를 최소화하는 조건에서 배합수의 양을 감소시킬 수 있다. 일반적으로 사용되는 감수제에는 리그닌(lignin), 리그노설포네이트(lignosulfonate), 나프탈렌 설포네이트 포름알데히드(naphthalene sulfonate formaldehyde), 설포네이트 포름알데히드(sulfonate formaldehyde), 반응성 폴리머(reactive polymer), 아미노-설포네이트(amino-sulfonate) 등이 있다(Duran et al., 2018). 특히 아미노-설포네이트의 경우 감수 효율을 최대 약 30%까지 증대시킬 수 있다고 보고된 바 있다. 감수제의 감수 효율은 감수제를 단독으로 사용하는 것 보다 다양한 종류의 감수제를 함께 활용할 때 그 효율이 크게 향상될 수 있다.
2.2.3 분산 저항제
분산 저항제는 뒷채움재 혼합물에서 재료 입자들의 분산을 억제하고 안정성을 향상시키는 첨가제에 해당한다(He et al., 2020). 주로 사용되는 분산 저항제에는 수용성 셀룰로스(water-soluble cellulose), 하이드록시에틸 셀룰로스(hydroxyethyl cellulose), 하이드록시프로필 메틸셀룰로스(hydroxypropyl methylcellulos), 폴리아크릴아마이드(polyacrylamide) 등이 있다. 분산 저항제는 뒷채움재의 유동성 저하를 방지하는 역할을 하며, 시멘트 수화 생성물을 흡착하여 중첩 효과(superposition effect)를 발생시켜 뒷채움재의 컨시스턴시(consistency)를 증진시킬 수 있다. 특히 수용성 셀룰로스는 시멘트 수화 생성물을 포집하고 구조를 형성하여 뒷채움재의 블리딩을 감소시키고 경화체의 굽힘 강도(flexural strength) 및 압축강도를 증가시키는데 유용하다.
2.2.4 기타 화학 첨가제
기타 화학 첨가제는 경화 촉진제(setting accelerator), 지연제(retarder agent), 초기 강도제(early strength agent), 수분 유지제(water-retaining agent), 미세 팽창제(micro-expansive agent) 등이 있으며 뒷채움재 성능 발현 목적에 따라 활용될 수 있다.
경화 촉진제로는 대표적으로 타알루미네이트(metaaluminate)와 같은 재료가 있으며 뒷채움재의 경화 시간을 단축시키는데 유용하게 활용될 수 있다(Zhang et al., 2018). 다음으로 지연제는 대표적으로 폴리인산염(polyphosphate), 타르타르산(tartaric acid), 붕산(boric acid) 등이 있으며 이는 뒷채움재의 열 방출 속도를 낮추고 시멘트의 수화반응 및 경화 시간을 지연시키는데 활용될 수 있다. 초기 강도제에는 트리에탄올아민(triethanolamine)과 같은 재료가 있으며 뒷채움재의 수화 시간을 단축시키고 초기 발현강도를 향상시킬 수 있다. 수분 유지제는 뒷채움재의 점성도를 향상시키고 수분 유지 능력(water-locking ability)을 개선시키며 양생 이후 균열 발생을 최소화하는데 활용될 수 있다. 마지막으로, 미세 팽창제는 경화된 뒷채움재 부피의 팽창을 유도하는데 활용된다.
3. 뒷채움재 내구성 평가를 위한 기본물성 분석사례
쉴드 TBM 굴착 시 세그먼트 라이닝과 배면 지반 사이 약 13~20 cm 간격의 공동(테일 보이드, tail void)이 발생하게 된다(Kim et al., 2009; Oreste et al., 2021). 뒷채움재는 이러한 배면공동을 충진 시킴으로써 터널 내 작용하는 수직응력 감소 및 수평응력 분산을 위한 역할을 한다(Belem and Benzaazoua, 2008). 이와 같이 뒷채움재는 주입 이후 경화하여 지반 지지력을 형성하는 재료에 해당하기 때문에 시간 경과에 따른 장기적 내구성을 확보하는 것이 필수적이다. 뒷채움재의 내구성은 압축강도, 밀도, 압축율, 투수계수 등의 기본물성으로 평가될 수 있다(Fig. 3). 본 논문에서는 뒷채움재의 내구성을 중심으로 기본물성과 관련된 문헌조사를 수행하여 분석하였다.
3.1 압축강도(compressive strength)
터널 배면공동 내 충진되는 뒷채움재는 시간 경과에 따른 경화 및 강도발현을 통해 지반 침하를 억제하여 터널의 역학적 안정성을 강화시키는 역할을 수행한다. 따라서 압축강도는 뒷채움재 성능 평가에서 가장 중요한 지표로 보고되고 있다(Lee et al., 2022). 이를 위하여 국내외에서 뒷채움재의 고결 시간에 따른 뒷채움재의 일축압축강도 기준들이 제시되고 있다. 일본 토목학회 터널 표준시방서쉴드공법편에 따르면, 뒷채움재는 양생 이후 1시간 강도는 0.1 MPa, 28일 강도는 2.5 MPa의 조건을 충족하도록 기준을 제시하고 있다(JSCE, 1996). 또한, 국내에서 서울특별시는 상기의 조건을 준용하여 일축압축강도 기준 뒷채움재의 양생이후 1시간 강도는 0.1~0.15 MPa, 1일 강도는 0.5 MPa 및 28일 강도는 3.0 MPa의 기준을 제시한 바 있다(Seoul Metropolitan Government, 2006).
Lee et al. (2022)은 3액형 무기질계 가소성 뒷채움재 및 LW (labiles wasserglass) 뒷채움재의 경화 시간에 따른 일축압축강도 측정 시험을 수행하였다. 일축압축강도시험은 KS L 5105 기준에 따라 수행되었으며, 시험편은 50 mm × 50 mm × 50 mm 정육면체 시편을 준비하였다(Fig. 4). 재령 1시간 이후 일축압축강도는 약 0.02~0.30 MPa 범위에 해당하였다. 재령 일수가 1일, 7일, 28일로 증가함에 따라 압축강도는 증가하는 경향을 보였으며, 재령 1일차 압축강도는 0.31~1.30 MPa, 재령 7일차 압축강도는 1.02~2.78 MPa, 재령 28일차 압축강도는 1.78~3.52 MPa의 범위에 해당하였다. 또한, 첨가제 배합비 증가에 따라 일축압축강도가 증가하였으며, 첨가제의 함량이 동일할 때, 시멘트 배합량이 증가하거나 벤토나이트 배합량이 감소함에 따라 일축압축강도가 증가하는 경향을 보였다.
Oreste et al. (2021)은 뒷채움재 시편의 경화에 따른 일축압축강도 시험을 수행한 바 있다. 시험편은 실제 북이탈리아 터널 굴착 현장에서 수행된 뒷채움재 주입을 모사하여 시험편을 A액(시멘트, 물, 벤토나이트, 지연제)과 B액(규산나트륨)으로 구성하여 배합을 실시하였다. 각 재료의 배합비율은 뒷채움재로 활용되는 일반적인 배합비를 참고하였으며, 각각의 함량은 단위체적(m3)당 시멘트 280~450 kg, 벤토나이트 30~60 kg, 물 730~860 kg, 지연제 3~5 kg, 규산나트륨 60~80 kg에 해당한다. 뒷채움재 시험편은 40 mm × 40 mm × 40 mm 정육면체 형태로 제작하였으며 양생 이후 1시간, 1일, 7일, 10일, 28일 시점의 일축압축강도를 측정하였다. 경화에 따른 일축압축강도는 양생 이후 1시간, 1일, 7일, 10일, 28일에 각각 0.1, 1.6, 2.6, 2.8, 3.0 MPa로 파악되었다(Fig. 5). 이러한 결과에서, 최종 강도인 양생 28일 이후 강도의 50%는 양생 1일 이후 빠르게 발현됨을 확인하였으며, 이에 따라 초기 강도 발현이 중요한 것으로 평가되었다. 또한, 양생 이후 10일 시점에서는 최종 강도의 93%가 발현되어 양생 10일 이후에는 뒷채움재의 내구성이 대략적으로 결정됨을 확인하였다.
3.2 밀도(density)
뒷채움재는 주입 이후 수화반응으로 인하여 경화체 내부에 공극이 발생하게 되거나 재료입자와 배합수의 분리가 발생할 수 있다. 이러한 뒷채움재의 주입 이후의 특성 변화는 뒷채움재의 밀도를 변화시키게 된다. 따라서 경화 진행에 따른 뒷채움재의 밀도를 평가하는 것은 내구성을 간접적으로 평가할 수 있는 중요한 물성에 해당한다. 이러한 밀도는 물-시멘트 배합비율 및 재료의 점도 특성과 밀접하게 관련되어 있음이 보고된 바 있다.
Wang et al. (2023)은 온도 변화 및 시멘트 뒷채움재의 물-시멘트 배합비율에 따른 밀도를 측정하였다. 물-시멘트 배합비율은 0.6, 0.8, 1.0, 1.2, 1.5 및 2.0으로 설정하였으며, 배합수의 온도는 20~90°C의 범위로 설정하였다. 시험편은 보통 포틀랜드 시멘트와 수돗물과 배합하여 제작하였으며, 밀도는 양생 이후 120분까지 측정하였으며, 시험편의 체적 및 질량값의 변화를 통하여 밀도를 평가하였다.
밀도 측정결과, 물-시멘트 비합비율이 증가할수록 뒷채움재의 밀도는 감소하였으며, 밀도의 증가속도는 증가하는 경향을 보였다(Fig. 6). 물-시멘트 배합비율이 0.6인 시험편에서는 양생 직후 및 120분 이후 시점의 밀도 값에 변화가 없는 것으로 평가되었다. 이와 반대로, 물-시멘트 배합비율이 2.0인 경우, 양생 120분 이후 밀도가 약 20% 증가하는 것으로 파악되었다. 또한, 배합수의 온도가 증가할수록 동일한 물-시멘트 배합비율에서 밀도 및 밀도 증가속도가 모두 높은 특성을 보였다.
3.3 압축율(compressibility)
뒷채움재는 주입 후 경화되면서 지반의 응력 및 변형을 감소시키는 역할을 하며, 뒷채움재가 액체에서 고체로 변화하는 고결에 따라 뒷채움재 경화체 내부에서 배수 및 압밀이 발생한다(Han et al., 2007). 또한, 뒷채움재가 주입되면서 뒷채움재 내부 수분이 배수되고 주변 지반의 압력으로 인해 체적의 압축이 발생하게 된다. 이러한 고결에 따른 뒷채움재의 압축 발생은 굴착 터널 지반의 침하 및 터널 내 누수를 유발시킬 수 있다. 따라서 뒷채움재의 구성재료, 경화 시간, 주변 지반 물성, 주입압력 및 지하수압 등에 의해 결정되는 압축율은 내구성 측면에서 중요한 물성에 해당한다.
Han et al. (2007)은 투수성이 높은 지반을 모사하여 뒷채움재 주입압에 따른 수분 이탈 및 이를 고려한 뒷채움재의 압축율 측정 실험을 수행하였다. 뒷채움재 주입 압력(Pg)을 0.15, 0.20, 0.25, 0.30 MPa, 지하수 압력(Pw)을 0, 0.05, 0.10 MPa로 설정하였다. 주입 압력 및 지하수 압력은 설정한 실험조건에서 체적압축율이 약 12% 미만으로 발생하는 것으로 파악되었다(Fig. 7). 또한 주입 압력이 지하수 압력보다 높은 경우, 시간 경과에 따른 압축율이 급격히 증가하는 경향을 보였다. 추가적으로 뒷채움재 주입 압력이 증가함에 따라 뒷채움재의 압축율이 증가함을 확인하였다. 지하수 압력이 0 kPa인 경우, 주입압력이 0.15 MPa에서 0.30 MPa로 증가할 때 압축율은 약 7.5%에서 12.5%의 범위인 것으로 파악되었다. 마찬가지로 지하수압이 50 kPa 및 100 kPa인 경우, 압축율은 5~10% 및 3~9%의 범위에 해당하였다.
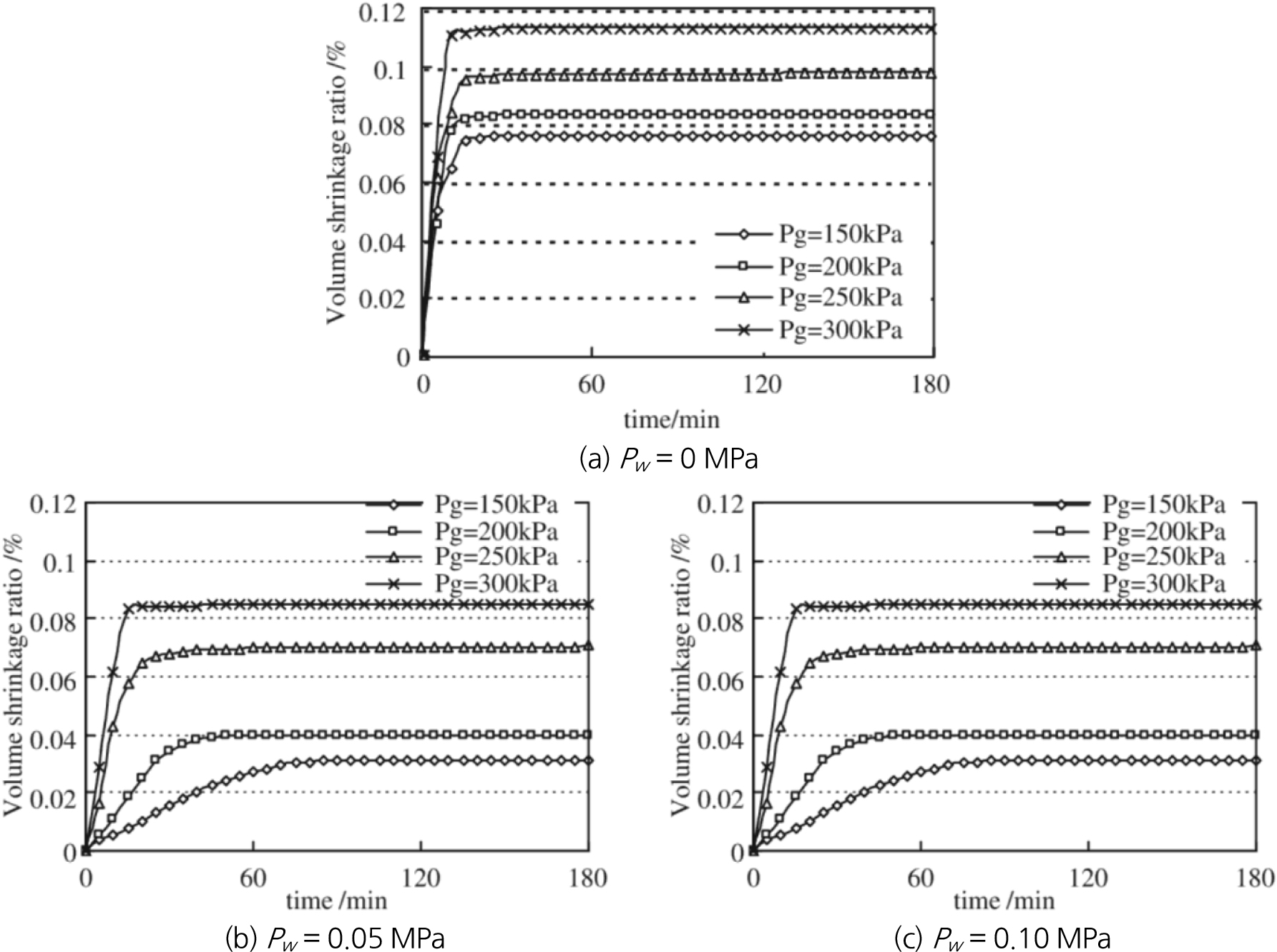
Fig. 7.
Results of compressibility according to curing time and ground water pressure (Han et al., 2007)
Kim (2010)은 규산계 및 무기계 가소성 뒷채움재의 압축율을 평가하였다. 규산계 뒷채움재는 국내 뒷채움 시공 현장에서 사용된 규산계 뒷채움재를 배합설계를 참고하여 A액(시멘트 250~350 kg, 벤토나이트 50~52.5 kg, 안정액 2.0~3.5 kg, 물 750~818 kg)과 B액(규산 80~100 L)을 준비 및 시편을 제작하였다. 또한 무기계 가소성 뒷채움재는 A액(시멘트 258 kg, 물 463 kg, 경화보조제 232 kg)과 B액(초기 강도제 386 kg, 물 437 kg, 경화촉진제 79 kg)으로 구성하였다. 압축율 실험은 시험편 제작 후, 14일 간 건조 양생을 진행하며 공시체의 직경 및 높이의 변화를 측정하여 시간경과에 따른 공시체의 체적변화를 통해 압축율을 산정하였다.
압축율 평가결과, 규산계 뒷채움재가 무기계 가소성 뒷채움재에 비하여 압축율이 큰 것으로 파악되었다. 규산계 뒷채움재 시험편에서는 양생 진행에 따라 시험편 표면에 균열이 다수 발생하였으며 부피의 변화가 크게 발생하였다(Fig. 8(a)). 반면, 무기계 가소성 뒷채움재 시험편의 경우 14일 경과 후에도 균열이 거의 발생하지 않았으며 부피변화 또한 미미한 것으로 파악되었다(Fig. 8(a)). 또한, 양생 7일 이후 규산계 뒷채움재 시편은 압축율이 21.9~40.3%로 평가되었다. 이와 반대로 무기계 가소성 뒷채움재 시편에서는 압축율이 약 99.1~102.4%로 평가되어 양생 진행에 따라 압축이 거의 발생하지 않은 것으로 파악되었다(Fig. 8(b)).
3.4 투수계수(permeability)
터널 굴착 과정에서, 기존에 존재하는 암반 절리 및 굴착에 의하여 생성된 새로운 절리를 통하여 배면공동 및 터널 내부로 지하수 침투가 발생할 수 있다. 이러한 터널 내부로의 지하수 유입은 터널 표면의 붕괴 및 구조적인 손상을 발생시킬 수 있다(Font-Capó et al., 2011). 또한 뒷채움재 내 지하수 유동을 통하여 전달된 염화물 이온, 황화물 이온, 산 등의 화학적 물질이 시멘트 기반 뒷채움재의 열화 손상을 유발할 수 있다(Yu et al., 2018). 따라서 뒷채움재 장기적 내구성 및 차수성능 확보를 위해서는 뒷채움재 경화에 따른 구조체의 공극구조 변화 및 이에 따른 투수계수 평가가 중요하다.
Yu et al. (2018)은 뒷채움재 배합비율, 양생일수 및 첨가제에 따른 투수계수 측정 실험을 수행한 바 있다. 시험편은 뒷채움재를 2분간 교반 후 직경 95 mm, 높이 10~15 mm의 시편을 제작하였다. 또한, 투수계수 측정 실험 장비 내 시험편을 투입하여 0.7 MPa의 수압을 적용시킨 후 양생 28일, 90일, 180일, 365일, 730일 후의 투수계수를 측정하였다(Fig. 9).
양생 진행에 따른 투수계수 평가결과 양생 이후 90일 경과 시까지 지속적으로 투수계수가 감소하는 경향을 보였다. 일반 포틀랜드 시멘트 재료를 사용하고 물-시멘트 배합비율이 0.4인 경우 투수계수는 양생 90일까지 초기에 비하여 약 53.5% 감소하였으며, 이후 양생 730일 시점까지 투수계수가 수렴하는 것으로 파악되었다(Fig. 10). 또한, 물-바인더 비율이 0.4 및 플라이 애시 30% 첨가된 시험편에서는 양생 365일까지 초기에 비하여 투수계수는 약 95% 감소하는 경향을 보였다. 이와 유사하게 물-바인더 비율이 0.4 및 플라이 애시 50%인 시험편에서는 같은 조건에서 투수계수가 약 98% 감소 후 일정한 값으로 수렴하는 특성을 보였다.
또한, Allan (2000)은 침투율을 측정하여 뒷채움재의 투수특성을 평가한 바 있다. 뒷채움재로 사용된 시멘트는 초가소화 시멘트와 보통 시멘트를 사용하였으며, 감수제는 나프탈렌 술폰산 나트륨(sodium naphthalene sulphonate)이 42% 첨가된 재료를 이용하였다. 물, 벤토나이트, 감수제, 시멘트, 모래 순으로 배합을 진행하였으며, 시험편은 직경 102 mm, 길이 70 mm의 크기에 해당하는 원주형 시편을 제작하였다. 투수계수 측정 시험은 ASTM D5084에 따라 실시되었으며 압력 구배는 207 kPa, 멤브레인 3축 구속압력 414 kPa으로 설정하였다.
투수계수 측정 시험 결과, 시멘트-모래 뒷채움재의 투수계수는 시멘트의 종류, 물-시멘트 배합비율에 따라 약 1.58 × 10-10 m/s로 측정되었다(Fig. 11). 또한, 시멘트-모래 뒷채움재의 물-시멘트 배합비율을 0.6으로 설정하였을 때 침투율은 양생 30일까지 큰 폭으로 감소하는 경향을 보였으며, 이후 30일에서 60일 동안은 수렴하는 특성을 보였다. 이후 양생일수가 60일 보다 증가하는 경우에는 침투율이 서서히 감소하는 것으로 파악되었다.
4. 지반 조건에 따른 뒷채움 시공사례: 내구성을 중심으로
뒷채움재는 지반의 종류 및 특성에 따라 지반조건에 따라 다양하게 활용될 수 있다. Liang et al. (2022)은 실제 터널시공 현장에서 수행된 뒷채움 시공사례 약 100여개 프로젝트를 정리하였으며, 지반종류 4가지(암반, 자갈, 모래 및 점토)에 대하여 요구되는 뒷채움재의 밀도, 양생 3일 후 압축강도 및 28일 후 압축강도에 대하여 연구를 수행한 바 있다.
Table 1은 4가지 지반 종류에 따라 제안된 뒷채움재 요구성능을 나타낸다. 뒷채움재의 밀도는 암반 및 점토층에서 약 1.72~1.93 g/cm3로 가장 높게 요구되었으며, 이외 지반에서는 상대적으로 낮은 약 1.47~1.84 g/cm3으로 제안되었다. 또한, 3일 후 압축강도는 암반, 모래 및 점토지반에서 약 0.5~0.6 MPa 이상 자갈지반에서 약 1.0 MPa 이상 요구되었다. 28일 이후 압축강도는 모든 지반조건에서 약 2.5 MPa 이상 확보되는 것이 바람직하다고 제안하였다.
Table 1.
Performance requirements of backfill materials (Liang et al., 2022)
Stratum | Density (g/cm3) | 3-day compressive strength (MPa) | 28-day compressive strength (MPa) |
Rock | 1.72~1.86 | >0.5 | >2.5 |
Gravel | 1.47~1.84 | >1.0 | >2.5 |
Sand | 1.69~1.86 | >0.6 | >2.5 |
Clay | 1.72~1.93 | >0.6 | >2.5 |
서로 다른 지반에서 활용된 뒷채움재의 물-바인더 비율(water/(cement+fly ash), W/B), 바인더-모래 비율((cement+fly ash)/sand, B/S), 벤토나이트-물 비율(bentonite/water, Ben/W) 및 시멘트-플라이 애시 비율(cement/fly ash, C/F) 사례는 Fig. 12와 같다. 우선 점토지반에서 물-바인더 비율은 그 활용 범위가 다른 지반에 비하여 넓은 경향을 보였지만 값 자체는 작은 특성을 보였다. 또한, 바인더-모래 비율과 벤토나이트-물 비율은 암반층에서 활용 범위 및 값이 가장 작았으며, 자갈지반에서 적용 범위가 가장 넓은 경향을 보였다. 마지막으로 시멘트-플라이 애시 비율의 경우 점토지반에서 활용 범위가 다른 지반에 비하여 가장 넓은 특징을 보였다.
또한, 서로 다른 지반에서 지하수 조건에 따른 뒷채움재 배합비율은 Fig. 13과 같다. 우선 암반에서 뒷채움재는 지하수 조건에 관계없이 시멘트-플라이 애시 비율 및 벤토나이트-물 배합비율은 유사한 경향을 보였다(Fig. 13(a)). 하지만 지하수가 존재하는 경우 물-바인더 배합비율은 약 0.5~1.0의 범위에 해당하여 지하수가 없는 조건에 비하여 상대적으로 낮은 특징을 보였다. 또한 벤토나이트-모래 배합비율의 경우 0.6~0.8로 상대적으로 높은 경향을 보였다. 다음으로 자갈 지반에서는 지하수 조건에 따라 벤토나이트-모래 배합비율이 가장 큰 차이를 보였는데, 지하수가 존재하는 경우 그 비율은 약 0.4~1.3으로 상대적으로 범위가 좁고 값이 작은 특성을 보였다(Fig. 13(b)). 모래 지반에서는 물-바인더 배합비율과 바인더-모래 비율이 가장 중요한 것으로 파악되었다(Fig. 13(c)). 지하수가 존재하는 경우, 물-바인더 비율과 바인더-모래 비율의 활용범위는 각각 0.1~1.0과 0.1~1.3으로 상대적으로 값이 작고 그 범위가 좁은 특성을 보였다. 마지막으로 점토 지반에서는 지하수 조건에 따라 시멘트-플라이 애시 비율과 바인더-모래 비율이 가장 두드러지는 차이인 것으로 파악되었다(Fig. 13(d)). 지하수가 존재하지 않는 경우 시멘트-플라이 애시 비율은 활용 범위가 약 0.1~2.4에 해당하였지만 지하수가 존재할 때에는 그 비율이 약 0.1~5.0까지 변화하는 특징을 보였다. 또한, 지하수가 존재할 때 바인더-모래 비율은 0.3~1.2에 해당하여 지하수가 존재하지 않을 때에 비하여 그 비율의 활용 범위가 넓은 특징을 보였다.
다음으로 지반의 강도와 같은 조건에 따라서도 요구되는 뒷채움재의 조건이 달라질 수 있다. Mohammadzamani et al. (2023)은 연약지반과 경암지반, 투수성이 높은 지반 및 낮은 지반에 따른 뒷채움재 배합을 제시한 바 있다. 연약지반의 경우, 터널 굴착 또는 이후 과정에 발생할 수 있는 지표면의 침하를 방지하기 위하여 초기강도 발현이 중요하기 때문에 뒷채움재의 경화시간 단축을 위하여 슬래그나 실리카 퓸 등과 같은 첨가제가 추가되는 것이 바람직하다고 제안되었다(Fig. 14). 이러한 과정은 뒷채움재의 경화 이후 재료의 부피 수축을 방지하여 내구성을 향상시키는데 효과적이다. 이외에도 경화시간을 단축시키기 위하여 모래를 포함시키거나 물유리, 벤토나이트를 함께 사용하기도 한다.
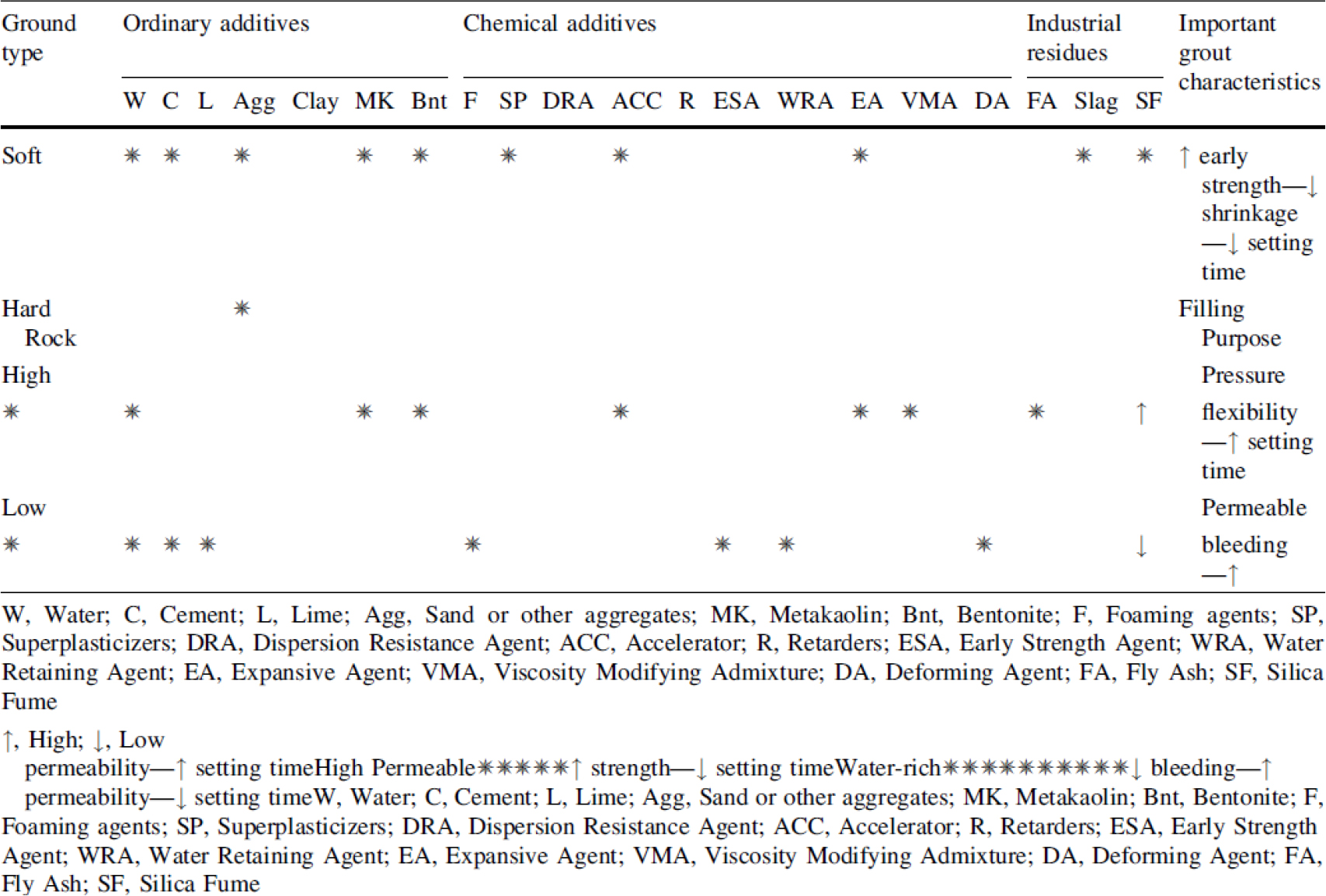
Fig. 14.
Suggestion of backfill material in tunneling based on ground conditions (Mohammadzamani et al., 2023)
이와 같이, 지반조건에 따라 다양한 뒷채움재를 주입 목적에 부합하도록 배합하여 활용하는 것이 중요하다. 하지만 뒷채움재의 압축강도, 밀도, 압축율 및 투수계수와 같은 내구성만을 증대시키기 위하여 배합설계를 실시한다면 뒷채움재의 유동과 같은 작업성(workability)가 감소할 수 있기 때문에 두 가지 성능을 함께 고려하는 것이 중요하다고 판단된다.
5. 결 론
본 연구에서는 쉴드 TBM을 이용하여 터널 굴착 시 활용되는 뒷채움재의 내구성 평가를 위하여 뒷채움재 구성을 위한 재료의 종류, 내구성 평가를 위한 기본물성 분석사례 및 지반 조건에 따른 내구성 중심의 뒷채움 적용사례에 대한 기술 현황을 분석하였다. 수행된 주요 결과는 다음과 같다.
1. 뒷채움재는 재료특성에 따라 주재료와 화학 첨가제로 분류할 수 있다. 주재료는 크게 시멘트, 벤토나이트, 골재 및 석회로 구성되며 화학 첨가제는 규산나트륨, 감수제, 분산 저항제 및 기타 화학 첨가제로 구성된다. 뒷채움재는 이러한 재료를 목적에 부합하도록 각 재료를 일정 비율로 배합하여 활용한다.
2. 뒷채움재는 터널 배면공동 내 주입 이후 경화됨에 따라 내구성을 중요하게 고려해야 한다. 내구성을 평가할 수 있는 뒷채움재 물성은 다양하게 존재하지만 압축강도, 밀도, 압축율 및 투수계수가 일반적으로 중요하게 고려되고 있다. 각 기본물성은 초기 강도 발현 및 장기적 내구성능 확보 목적에 따라 설계되는 것이 중요하다.
3. 뒷채움재 내구성 향상을 위해서는 지반 조건이 중요하게 고려되어야 한다. 지반조건은 암반, 자갈, 모래 및 점토와 같은 지반의 종류와 연약지반 또는 안정지반과 같은 특성에 따라 분류할 수 있으며, 각 조건에 따라 뒷채움재의 배합설계 및 주입 시공이 필수적이다. 뒷채움재의 내구성을 향상시키기 위하여 다양한 첨가제가 활용될 수 있지만 내구성만을 고려하는 경우 유동성, 블리딩 및 점성도와 같은 작업성이 저하될 수 있다. 향후 현장에서는 이러한 내구성 및 유동성을 함께 고려하여 뒷채움을 시공하는 것이 중요할 것으로 판단된다.